
A brief explanation of the lost wax process continued...
Investing: The wax casting is cleaned and coated with up to 7 layers of liquid refractory ceramic in a temperature and humidity controlled environment. The investing process can take up to a week as each coat must dry before the next layer is applied.
Firing: The ceramic mould is fired in a kiln, which bakes the ceramic and melts out the wax, leaving a cavity in its place (thus the term 'lost wax' process).

Casting: The ceramic mould is preheated, then filled with molten bronze at a temperature of 2100 degrees fahrenheit. Bronze is an alloy, primarily copper…up to 96%

Divestment: After the bronze has cooled, the ceramic mould is carefully hammered and chiseled, broken away, revealing the sculpture within. The bronze is sandblasted and the gates are power-cut off.

Chasing: Then the gates and sprues are ground away, these areas are blended into the casting. Next comes the balance of the chasing process: levelling, grinding core pins, welding, sanding, filing, die grinding, bead blasting, rough buffing and quality control.

Back | More...
Investing: The wax casting is cleaned and coated with up to 7 layers of liquid refractory ceramic in a temperature and humidity controlled environment. The investing process can take up to a week as each coat must dry before the next layer is applied.
Firing: The ceramic mould is fired in a kiln, which bakes the ceramic and melts out the wax, leaving a cavity in its place (thus the term 'lost wax' process).

Casting: The ceramic mould is preheated, then filled with molten bronze at a temperature of 2100 degrees fahrenheit. Bronze is an alloy, primarily copper…up to 96%

Divestment: After the bronze has cooled, the ceramic mould is carefully hammered and chiseled, broken away, revealing the sculpture within. The bronze is sandblasted and the gates are power-cut off.

Chasing: Then the gates and sprues are ground away, these areas are blended into the casting. Next comes the balance of the chasing process: levelling, grinding core pins, welding, sanding, filing, die grinding, bead blasting, rough buffing and quality control.

Back | More...
Photograph by Gina Taro
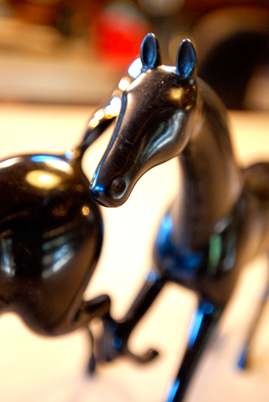